When it comes to choosing between seamless and welded pipes, there are pros and cons for each option. Seamless pipes offer several notable advantages while welded counterparts have their own set of benefits.
In this article, we will look at the key differences between these two types of piping to help you make an informed decision about which one is best suited for your project. Well, weigh up the pros and cons from both sides so that you can assess their suitability for your requirements.
By understanding the particular features of SMLS pipes compared to welded versions, we hope that you will be able to confidently choose the right pipe for your application.
Pros:
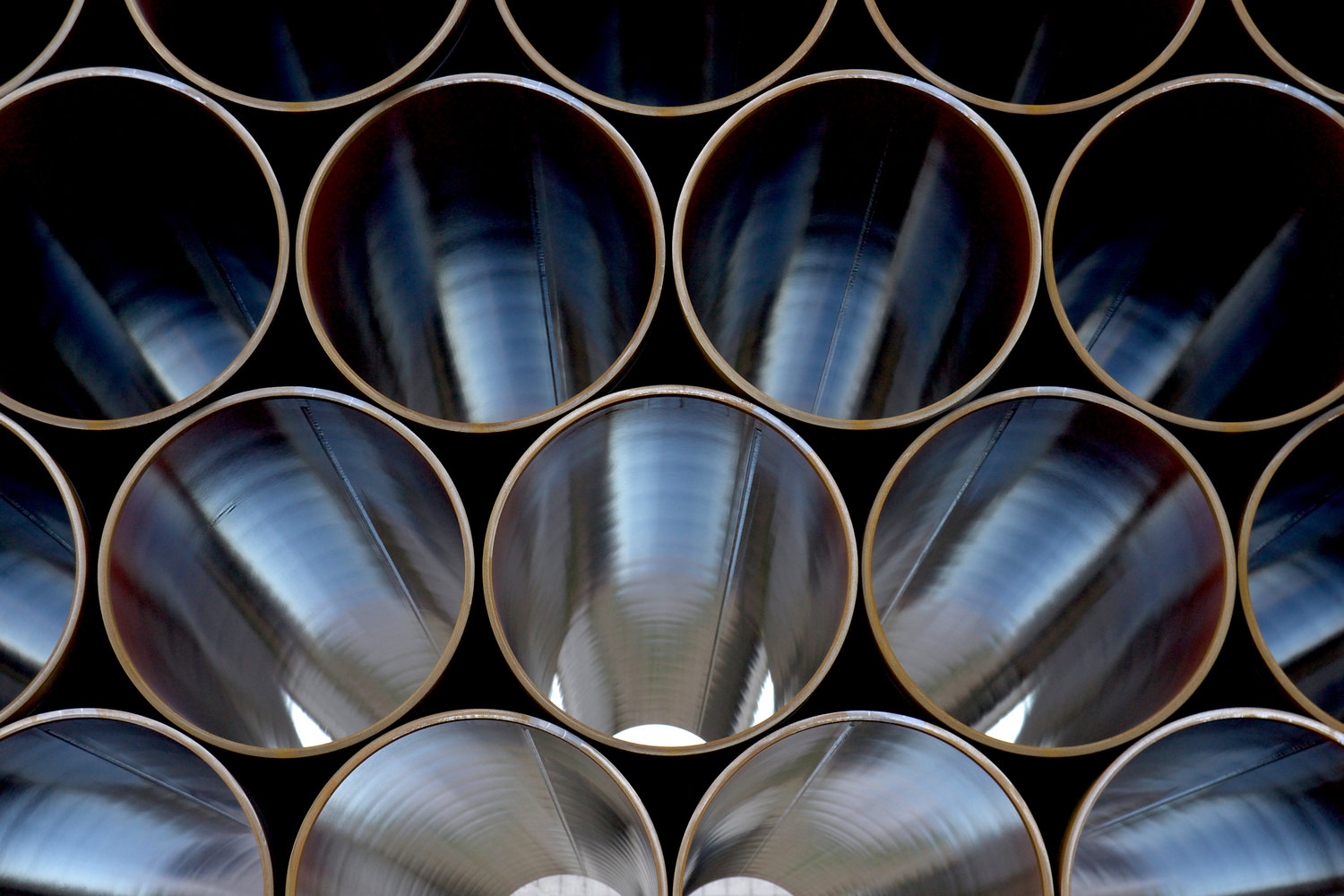
1. Lower Cost
When it comes to cost, SMLS pipes offer a lower price point than their welded counterparts. This is because they are less complex and can be manufactured more quickly.
Additionally, SMLS pipes require fewer raw materials than their welded counterparts which further reduces costs. Furthermore, since the process of manufacturing SMLS pipes is simpler and faster, there are also fewer labor costs associated with them as compared to welded pipes.
Overall, this makes SMLS an attractive choice for those looking to save on production expenses without sacrificing quality or performance.
2. Quicker Installation Times
SMLS pipes offer a much quicker installation time than their welded counterparts. This is because they have fewer parts that need to be assembled and don\’t require any welding, cutting, or heating.
As such, this makes them ideal for projects where speed is of the essence as there will be less preparation and manpower needed to install them. Furthermore, SMLS pipes can also save money by reducing overall project costs due to their easy installation process compared with welded piping systems. The fact that these pipes are designed as one piece also means that they are inherently stronger than those made from individual pieces which adds to their durability and reliability over long-term use.
Lastly, SMLS pipes tend not to corrode over time like other materials, making them an even more attractive choice for many applications where corrosion resistance is essential.
Cons:
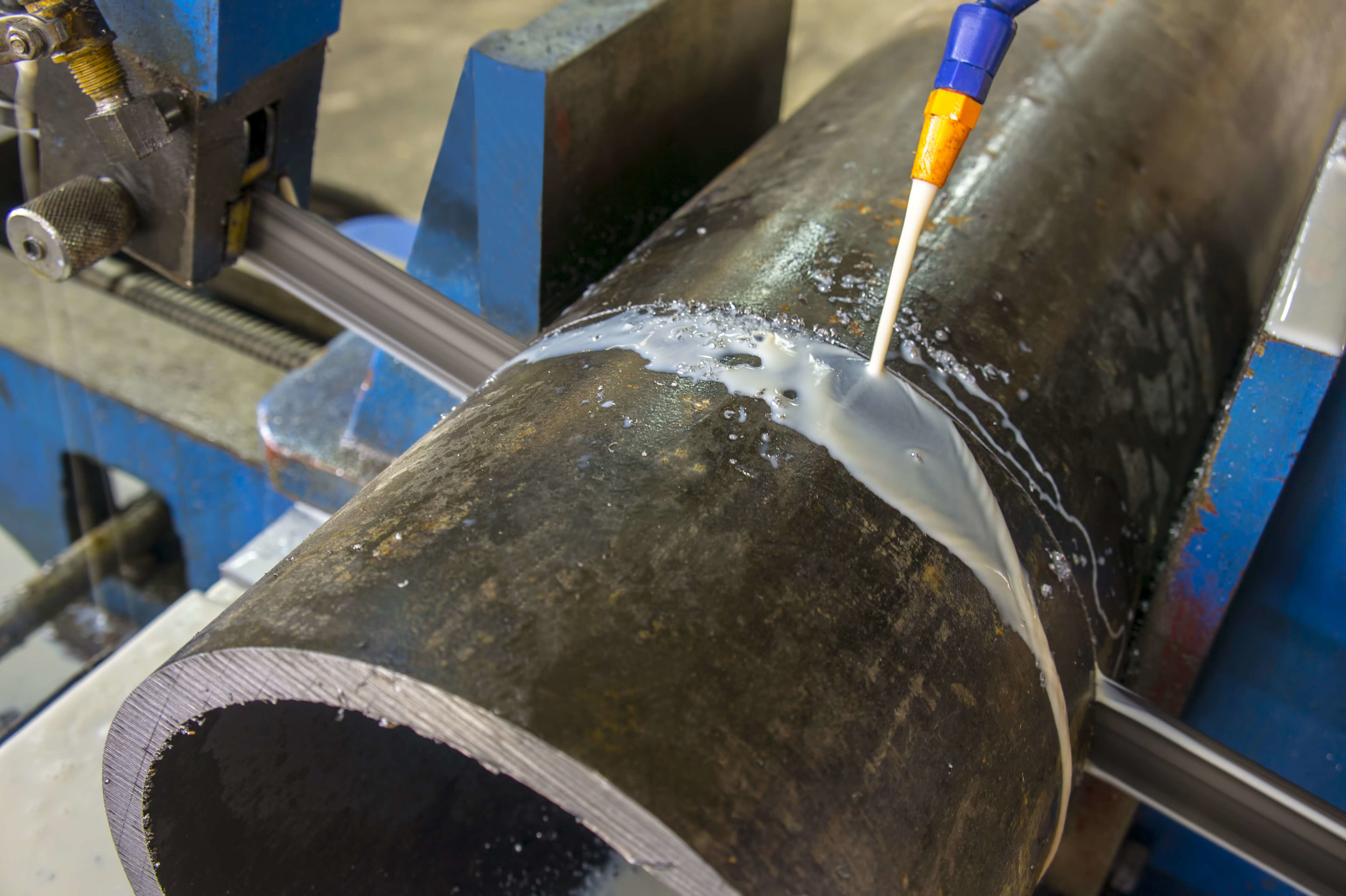
1. Limited Lengths Available
When it comes to comparing seamless (SMLS) pipes with their welded counterparts, length is a key factor. Seamless pipes are available in limited lengths due to the difficulty of producing them without seams using conventional manufacturing processes.
Welded pipes can be made to order in any length, making them more versatile for many applications. However, this advantage also brings certain disadvantages such as increased cost and weight that need to be taken into account when selecting a pipe type for an application.
Both types of pipe have pros and cons depending on the situation; therefore, it is important to understand the limitations of SMLS pipes when considering their use in comparison with welded alternatives.
2. Difficult to Fabricate Complex Fittings or Shapes
When it comes to fabricating complex fittings or shapes, seamless pipes have a definitive advantage. The ability to produce uniform parts with consistent walls and no welds makes SMLS pipes ideal for creating intricate shapes.
For example, long radius bends can be produced in one piece without having to build up layers of material from multiple welded sections. This saves time and money when compared to the welding of more complex pieces together.
Additionally, more precise tolerances can be achieved through the use of this method which is essential for certain applications such as aerospace components where tight specifications must be met. On the other hand, some types of fitting may not be possible with SMLS so there are trade-offs between these two methods when considering fabrication complexity.
Conclusion

When it comes to pipes, SMLS Pipes offer distinct advantages over their welded counterparts. They are easier to install, are more cost-effective, and can be produced in much shorter time frames than welded pipes.
In addition, they are lightweight and require less maintenance due to their uniformity of wall thickness throughout the pipe length which reduces the risk of corrosion or wear and tear over time. Despite these benefits, Welded Pipes may still be preferred for certain applications due to superior strength or other considerations.
It is important that engineers carefully weigh all the pros and cons when selecting between SMLS Pipe and Welded Pipe for a given project.