The future of fabrication is here, and its changing the way we approach laser cutting technology. From improved accuracy to faster speeds, advancements in this area are revolutionizing manufacturing processes.
With a plethora of innovative developments coming to the fore, it’s no surprise that laser cutting is becoming an increasingly popular choice for many businesses. In this article, we will explore some of these revolutionary innovations and how they can benefit your operations.
We will also look at why laser cutting continues to be such a reliable and efficient method for fabricating products or components with precision and speed. So buckle up as we dive into the exciting world of laser-cutting technology!
Exploring the Advantages of Laser Cutting for Fabrication

Exploring the Advantages of Laser Cutting for FabricationLaser cutting technology has revolutionized the fabrication industry. Its ability to quickly, accurately, and consistently cut intricate shapes out of a variety of materials makes it an invaluable tool for fabricators looking for increased efficiency in their operations.
With advances in laser cutting technology comes more precise results with fewer errors which not only reduces labor costs associated with manual processes but also helps to increase quality control and product consistency across orders.
Additionally, less material is wasted when using lasers as they are capable of performing complex cuts or designs with minimal waste material left behind after completion – providing substantial cost savings over traditional methods like sawing or die stamping while still producing high-quality parts.
Lastly, these machines provide improved safety protocols since humans arent required near the operating machinery – making them ideal investments for businesses that prioritize worker safety alongside productivity gains.
All these factors combined make laser cutting an obvious choice when considering options for improving manufacturing efficiency while simultaneously increasing output quality levels accordingly!
Utilizing New Technologies to Enhance Manufacturing Processes
As the world continues to move into the future, manufacturers are turning to new technologies to enhance their fabrication processes. Laser cutting technology is a prime example of this, offering precision and accuracy that was once impossible with traditional methods.
This technology uses an intense beam of light to cut through materials such as metal or plastic quickly and cleanly. With laser cutting technology, manufacturers now have access to more efficient production times while also reducing labor costs associated with manual processing techniques.
Additionally, laser cutting can produce intricate designs and complex shapes that would be difficult or impossible using other means.
By incorporating advanced tools like lasers into their manufacturing process, companies can create higher quality products while optimizing efficiency and safety in their operations.
The possibilities for utilizing new technologies such as laser cutting within the realm of production are endless; its just up to us to adapt accordingly so we can continue pushing our industry forward into the future!
Understanding How Advanced Laser Cutting Techniques Impact Manufacturing Efficiency
When it comes to understanding how advanced laser cutting techniques impact manufacturing efficiency, there are several key factors that must be taken into account. The speed and accuracy of the laser cutter is one of the most important considerations when selecting a machine for fabrication projects.
Laser cutters provide greater precision than traditional methods, meaning fewer mistakes in production and less material waste overall. Additionally, these machines can process complex shapes with intricate details more quickly than manual processes which leads to faster lead times on orders for fabricators.
Furthermore, automated processes also offer improved safety protocols since human labor isn’t required near the operating machinery – an important factor for businesses looking to invest in new technologies while still ensuring worker safety.
Ultimately, by carefully analyzing their needs and evaluating all available options within this rapidly evolving industry, businesses can find the best solution for their specific application – whether its a single job or ongoing large-scale production runs – so they can maximize efficiency and minimize costs going forward into future operations as needed!
Conclusion
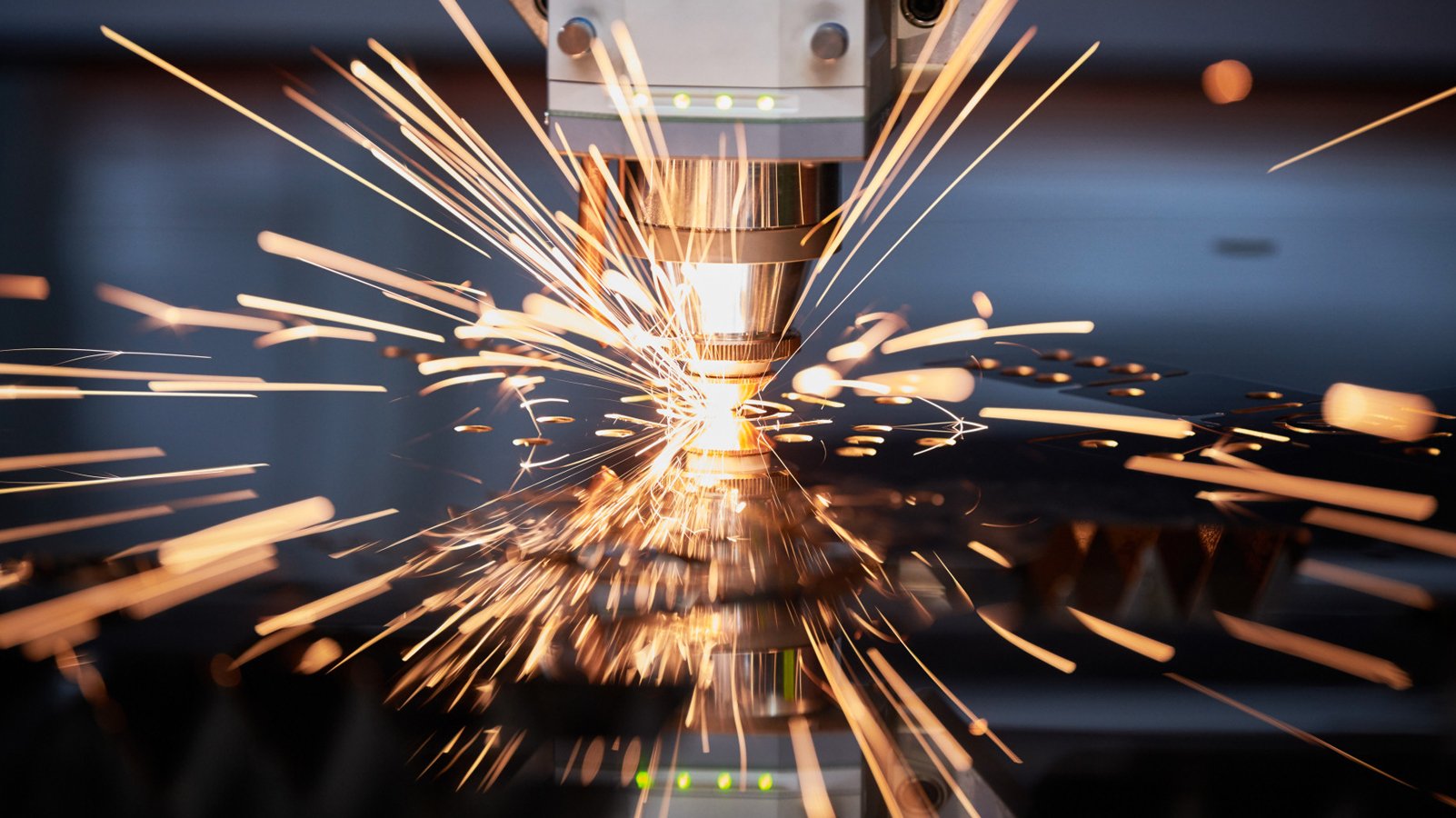
The advancements in laser cutting technology have created a wide range of possibilities for the future of fabrication. From improved safety and accuracy to cost savings, laser cutting is transforming how fabricators approach projects.
Laser cutters are also becoming increasingly more versatile with features like handheld laser welding machines from ZL Tech Laser that make it easy to quickly and precisely join materials without ever having to leave the shop floor.
As this technology continues to evolve, we can expect even greater capabilities with increasing precision and accuracy as well as increased versatility for fabricators everywhere.