Many industries require specialized chemical products tailored to their exact needs and processing methods. Off-the-shelf chemicals have standard concentrations and properties that may not suit unique applications. Customizing formulations and production to match precise specifications enables better performance and efficiency.
For example, a battery maker works with a chemical company to develop custom electrolyte mixtures. The customized electrolyte offers conductivity and viscosity perfectly aligned to that client’s battery technology. Such collaborative projects yield materials and ingredients that fit seamlessly into existing flows rather than requiring process changes to fit generalized chemicals.
Drivers Behind the Growth in Custom Chemicals
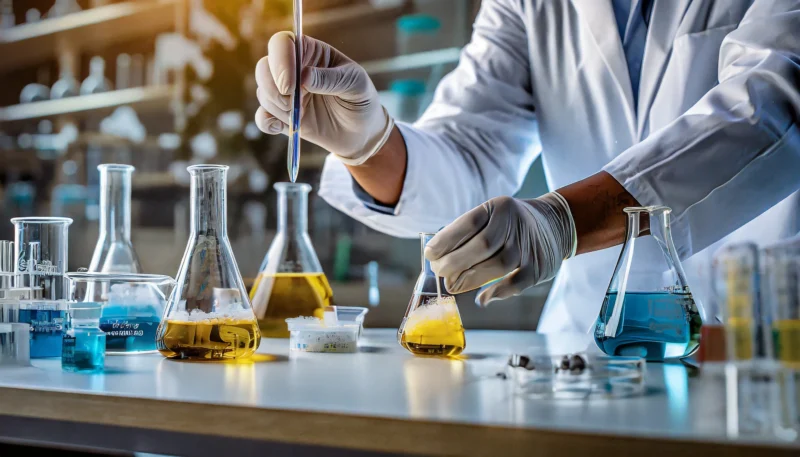
Several factors contribute to the rising demand for custom chemical solutions:
- Proprietary Advantage – Formulations created for a single client prevent competitors from easily replicating production methods and materials, protecting intellectual property. Custom chemicals with proprietary value strengthen supply chain security.
- Process Optimization – Matching chemicals to existing equipment, workflows and infrastructure squeezes out more yield and quality without costly retrofitting. Performance gets maximized when all materials sync together.
- Supply Chain Control – Securing customized ingredients from select suppliers reduces reliance on fluctuating commodity markets for raw materials. This insulates companies from shortages or price swings.
Companies such as Trecora, which offers custom chemical processing services, continue to expand their capacity to manage the growth as more manufacturers realize the benefits of specialty chemicals tailored to individual operations.
Creating Strategic Chemical Partnerships
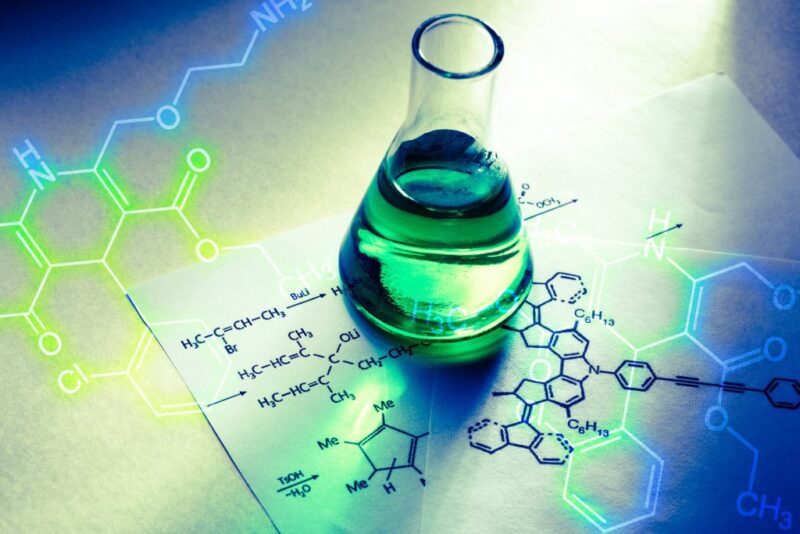
Cross-industry collaboration marks a shift from the traditional client-supplier relationship toward strategic partnerships. Customers work closely with chemical specialists to co-engineer solutions from concept through commercial-scale production. Initial consultation identifies key requirements the custom chemical must meet, considering functionality, purity, handling, regulatory issues and cost.
Ongoing teamwork optimizes the production process before undertaking final large-volume manufacturing. Manufacturers gain flexibility, expertise and customized chemicals to sharpen competitiveness. Meanwhile, suppliers better understand client objectives to anticipate needs amid shifting markets. The result is enduring, cooperative business relationships.
Open information sharing is crucial, so manufacturers provide details needed to translate performance goals into chemical attributes and production methodology. Clear, ongoing dialogue thereby turns tentative product ideas into tangible formulations.
Challenges in Delivering Custom Chemicals
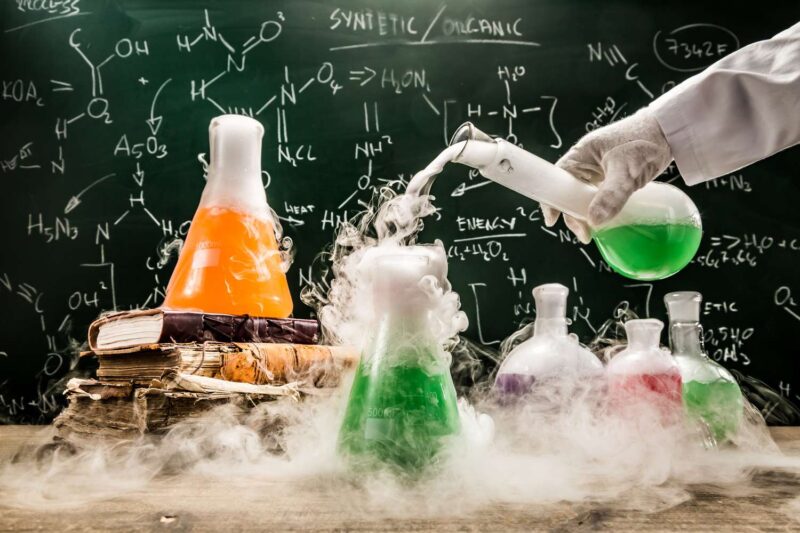
However, custom projects present unique hurdles, including:
- Narrow Focus – Because formulations target a single client’s needs, production volume remains relatively low, limiting potential revenue. Solutions must therefore emphasize high-value performance areas that justify added investment. Profitability relies on producing chemicals that significantly advance competitive positioning.
- Confidentiality – Protecting proprietary client data, custom formulations and production techniques requires vigilant security measures within facilities and staff. Breaches risk intellectual property losses that negate exclusivity.
- Variable Conditions – Custom requests might require adapting equipment and methods beyond their normal operating range, increasing quality control risks. Careful planning minimizes this variability by optimizing chemical attributes for production using preferred reactors and processes.
- Evolving Specifications – As client needs change over a project’s duration, custom solution specifications might also shift, complicating development. Both parties avoid mission creep by clearly defining requirements upfront with an expectation of reasonable adjustments, not scope changes.
Conclusion
Industry analysts forecast robust growth in custom chemicals as manufacturers continue prioritizing specialization and made-to-order capability. Tighter environmental regulations may also drive more custom chemical usage as companies modify formulations to comply with changing emissions and chemical handling rules.
Meanwhile, improving collaboration tools makes it easier for clients and chemical producers to securely partner on creating the ideal proprietary solutions. Further adoption of automation and expert systems can also help manufacturers adjust nimbly to customer needs. The overall result is a chemical supply chain ever more responsive to specialty demands, ultimately speeding innovations in downstream products that benefit end consumers.